تسمه ترانس مقطعی - تسمه ترانس صاف - تسمه ترانس چهار پهلو-تسمه فابریک - تسمه ماشینکار .- تسمه نوردی - تسمه فولادی - تسمه استیل- تسمهspk - تسمهspkr - تسمهspknl .- تسمهmo40- تسمه آموتیت - تسمهck45 - تسمهcmsk
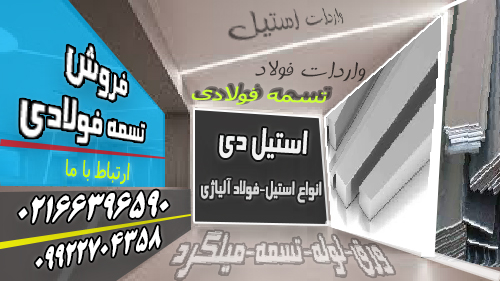
تسمه ترانس
در صنایع گوناگون به خصوص صنایعی که از مصالحی با دقت بالا مصرف دارند بیشتر از تسمه های آهنی ترانس شده استفاده میکنند .
انواع دیگر نوارهای فولادی مانند تسمه ماشینکاری و یا تسمه نوردی به عنوان ماده اولیه تسمه ترانس هستند .
بدین ترتیب که ماده اولیه در یک پروسه ماشینکاری از قالب های مورد نظری که از قبل موجود است.
و یا برای ابعاد مورد نیاز طراحی گردید عبور داده میشود و به سایز مناسب می رسند .این ابعاد با دقتهایی نظیر دهم میلیمتر میباشد . جنس قالبها به دلیل مقاومت مناسب در برابر آهن از تنگستن در نظر گرفته میشود. تا مقاومت لازم را در برابر آن جهت اصلاح ابعاد داشته باشد
تسمه فابریک
این محصول یک پروفیل فولادی میباشد که در کارخانه با بهره گیری. از روش نورد گرم و با استفاده از مواد اولیه بیلت(شمش). فولادی پس از حرارت دهی در کوره نورد و رسیدن به دمای مشخصی وارد پروسه نورد میشود و آهن خمیری شکل با عبور از دروازه های معینی در انتهای کار به شکل یک مقطع مستطیل شکل در می آید.
تسمه نوردی
تسمه نوردی هم یک مقطع طویل فولادی مستطیل شکل است . تسمه نوردی بر اساس روش تولید دقیقاً شبیه تسمه فابریک است. اما در تفاوت تسمه نوردی با نوع دیگر میتوان گفت .: غیر از اینکه تسمه های نوردی عمدتاً در صنایع کوچکتر تولید میگردد .،
در تولید تسمه های نوردی عموماً از شمش به عنوان ماده اولیه استفاده نمی شود.
و به جای آن از مواد اولیه دیگری استفاده میشود این مواد اولیه بر اساس سیاست تولید کننده انتخاب میشود. که قصد دارد محصول با کیفیت تری تولید کند و بازار مناسبی برای ارائه محصول داشته باشد و یا اینکه با سیاست ارزان تر تمام کردن محصول خود بازاری برای خود ایجاد نماید .
بهترین مواد اولیه جهت تولید نوارهای نوردی عبارت است از
: برش ورقهای فولادی ST-۳۷ (فولاد نرمه ساختمانی) .و یا استفاده از مواد اولیه میان خطی تولید بیلت (شمش) است .که به ابعاد مناسب جهت قرارگیری در پروسه تولید برش داده میشود. و در پروسه نورد قرار میگیرد. با توجه به اینکه برای تولید تسمه نوردی این مواد اولیه قیمت بالاتری نسبت به سایر مواد دارند .،
تسمه نوردی تولید شده بر پایه این مواد اولیه
از قیمت بالاتری برخوردار است. از سوی دیگر برخی دیگر از تولیدکنندگان با استفاده از مواد اولیه نا مرغوب. مثل میلگردهای AIII و ... اقدام به تولید این محصولات می کنند .که این انواع محصول به دلیل استفاده از مواد اولیه پرکربن از سختی بسیار بالایی برخوردار هستند.
قیمت در پروسه تولید
با توجه به این که استفاده از مواد اولیه نامرغوب باعث کاهش قیمت تمام شده برای تسمه نوردی میگردد .لذا شاید شائبه گران فروشی در ذهن خریدار برای دیگر محصولاتی که از مواد اولیه مناسب .در پروسه تولید استفاده کرده اند ایجاد گردد.
تسمه یک حلقه از مادهای انعطافپذیر است
که برای ایجاد پیوند مکانیکی و انتقال انرژی بین دو یا چند شفت استفاده میشود. تسمهها به دور پولیها پیچیده حلقه مینند.
در یک سامانهٔ دارای دو پولی ممکن است .هر دو پولی در یک جهت به گردش درآیند یا تسمه به صورت ضربدری باشد تا جهتشان مخالف گردد.
به عنوان یک عامل حرکت ، تسمه نقاله یکی از کاربردهای تسمه است که در آن از تسمه برای حمل بار بین دو نقطه استفاده میشود.
تسمه فولادی می تواند هم به صورت فابریک
و یا از ورق فولادی و یا ورق گالوانیزه ساخته شود. تسمه ها از پر کاربردترین مواد و قطعات در تمامی صنایع و خصوصا صنایع بسته بندی ، می باشند.
تسمه های فولادی دارای کاربردهای زیادی در صنعت می باشد که برخی از موارد کاربرد این محصول در مصارف ساختمانی و صنعتی. ، سازه های فلزی ، تیرچه های فلزی خود ایستا (کرومیت ، گریتینگ ، گاردریل و تولید مقاطع باز فولادی به روش پرس برک و… می باشد.
کاربرد تسمه فولادی و گالوانیزه
هرچند که نوارهای فولادی و گالوانیزه تقریبا در تمامی صنایع کاربرد دارند. اما برای موارد خاص می توان از آلیاژهای دیگر فلزی نیز استفاده کرد. به عنوان مثال تسمه مونل.، تسمه آلومینیوم و … جایگزینی برای این نوع تسمه ها هستند.
کاربرد تسمه های فولادی در داخل جانِ تیرآهن و برای وصله کردنِ ان و یا در ساخت بادبند .و اتصالِ انها به هم مورد استفاده قرار می گیرد.
همچنین در صنعت درب و پنجره نیز، برای یک دست کردن سطوح و پر کردنِ فضای خالی بکار برده می شوند.
فولادی استیل
تسمه فولادی از استیل سری ۳۰۰ ساخته شده و تسمه فولادی ۳۰۴ مهمترین محصولی است که از مجموعه تسمه های استیل عرضه می شود .
تسمه استیل یک ورق استیل صیقل شده با ضخامت کم می باشد که در ضخامت های مختلف ساخته می شود.
طول تسمه استیل یا به صورت سفارشی خواهد بود و یا رول های آماده ای است که در بازار عرضه می شود.
کاربرد تسمه فولادی
تسمه های فولادی دارای کاربردهای زیادی در صنعت می باشد .که برخی از موارد کاربرد این محصول در مصارف ساختمانی و صنعتی. ٬ سازه های فلزی ٬ تیرچه های فلزی خود ایستا ( کرومیت ) ٬ گریتینگ ٬ گاردریل و تولید مقاطع باز فولادی به روش پرس برک و… میباشد.
تسمه فولادی گالوانیزه
کابل برق و کابل تلفن
تسمه فولادی استنلس استیل
در صنایع کابل برق و تلفن ، لوازم آشپزخانه .، لوازم چاقو سازی ، وسایل جراحی ، صنایع اتومبیل سازی ، صنایع لوله سازی و در سازی.
تسمه فولادی سرد نورد
کابل برق و تلفن ، کابل مخابرات ، صنایع اتومبیل سازی. ، صنایع دوچرخه سازی ، ترانسفورماتور ، لوازم خانگی ، رادیاتور.
تسمه های فولادی گرم نورد:جهت استفاده در صنایع بسته بندی ، درب و پنجره.
استیل دی (Steel day)
با سالها تجربه در زمیه عرضه و توزیع انواع استیل بگیر و استیل نگیر. و همچنین انواع فولادهای نسوز و فولادهای دریایی و ساختمانی توانسته است رضایت مشتریان خویش را فراهم نماید. زیرا کارشناسان مجرب استیل دی آماده اند تا در زمینه مشاوره و ارائه دادن بهترین پیشنهادات خرید محصول به مشتریان عزیز خدمات رسانی نمایند.
صنعتگر محترم و گرامی از اینکه استیل دی را جهت خرید فولاد آلیاژی مورد نیاز خویش انتخاب می نمایید از شما سپاسگزاریم.
تمام محصولات استیل دی بر حسب نوع کالا دارای گواهینامه ها و آنالیزهای معتبر داخلی و خارجی می باشند.
ارتباط با ما:
09922704358
02166396590
واتس آپ: 09922704358
ارتباط با ما در شبکه های اجتماعی (با کلیک بر روی لینک های زیر به ما بپیوندید)
https://t.me/steel_day تلگرام
https://www.instagram.com/steel_day.ir اینستاگرام
https://twitter.com/MDlakan توییتر
pinterest پینترست
ایمیل: steelday.foolad@gmail.com
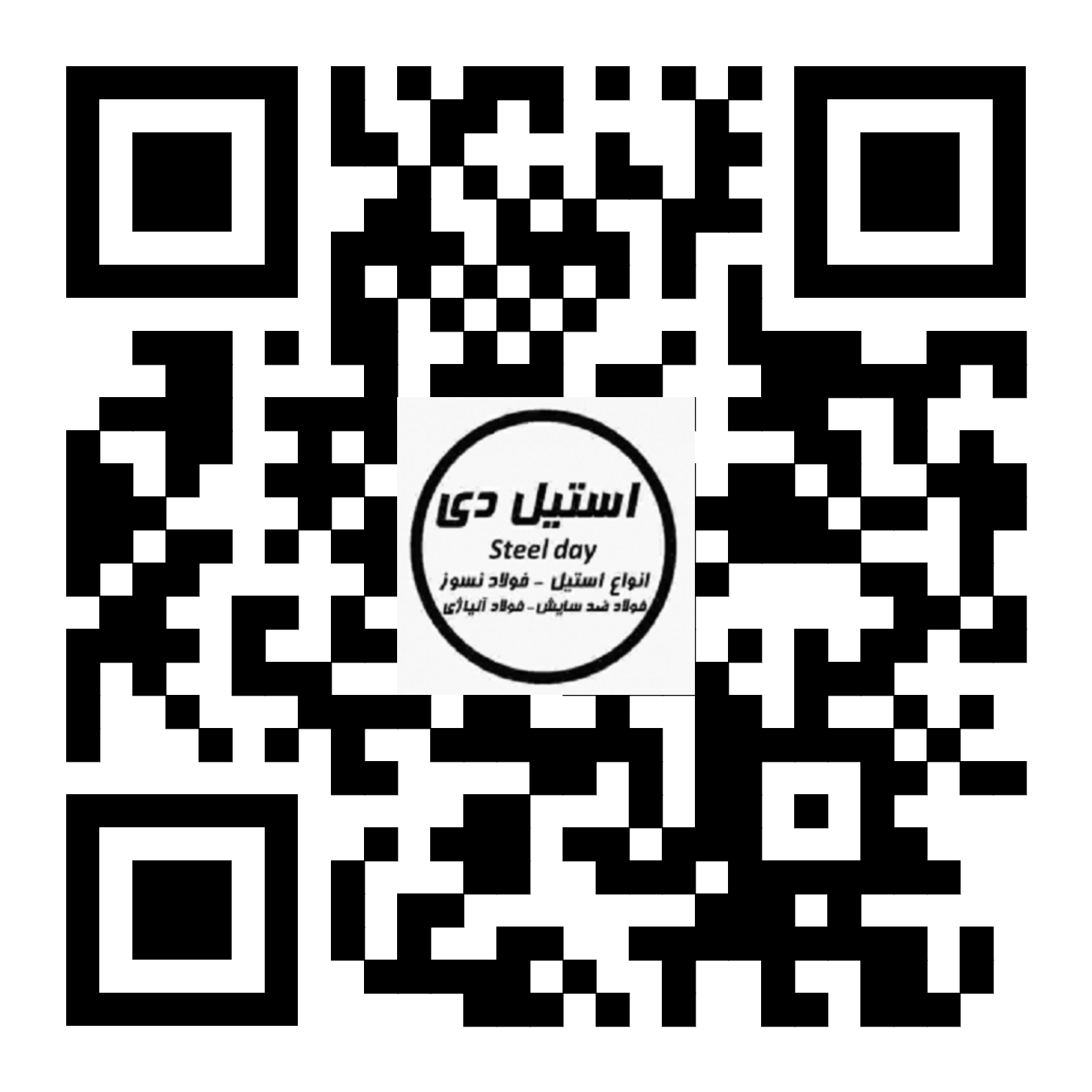